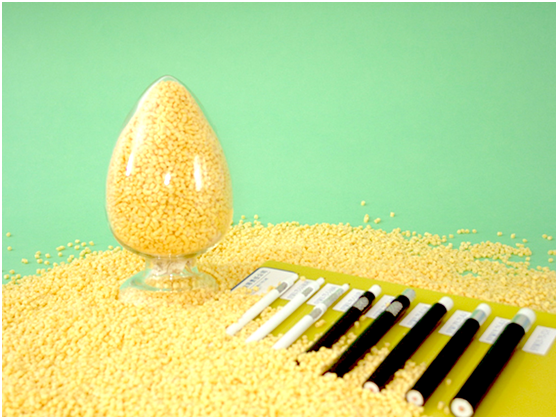
The foaming nucleating agent has the characteristics of stable and uniform dispersion in the insulating material. The highly effective dispersant in the carrier resin has good compatibility with the matrix resin. With the help of screw shear and mixing, it can rapidly spread in the polymer melt, thus promoting the nucleating agent to form evenly distributed “hotspots” in the polymer melt, and locally reducing the surface of the melt Tension and melt viscosity, so as to achieve the purpose of fine foam. After adding foaming nucleating agent, the processing temperature of the insulating material is no different from that of the insulating material itself, and the extrusion fluidity of the material is better.
Foaming Nucleating Agent Consists Of Activator is designed to be extruded with LDPE or HDPE gas injection compounds for processing physical foaming insulated coaxial cables. It is normally added at 1-3% masterbatch concentration into a blend of 60-80% HDPE and 20-40% LDPE.
While the exact temperature profile required will depend upon the screw design and construction being made, the following extrusion temperature profile represents a good starting point:
Feed Zone : 140 ℃to 150 ℃
Transition Zone : 170 ℃to 180 ℃
Gas injection point : 170℃ to 190 ℃
Metering Zone : 140℃ to 170 ℃ (depending on insulation diameter)
Crosshead and die : 130℃ to 190 ℃ (depending on insulation diameter)