Foaming can be divided into two ways: physical foaming agent and chemical foaming agent. 1. Physical foaming is to select HDPE with appropriate molecular weight and use special N2 compression equipment N2 to mix it into the screw cylinder for melting and melting in the material. It is stirred evenly by the screw and produces large pressure and expands instantly after extrusion to form light porous foaming PE. 2. Chemical foaming is to add foaming agent to HDPE, whose main component is generally ammonia compound At high temperature, it will decompose and produce N2. The smaller external mold will make the larger pressure in the die. When the pressure is released after extrusion, the N2 in the die will expand into pores and become foamed PE. Because the foaming agent is added in it to achieve the foaming effect by chemical reaction, it is called chemical foaming. The purpose and advantages of second foaming 1. Making the product lightweight can reduce the material cost but reduce the material cost Dielectric coefficient is the main purpose. 2. Small dielectric constant, low dielectric loss, low high-frequency attenuation, stable performance, good waterproof, moisture-proof and bending, small cable outer diameter, long service life and other advantages. 3. Good mechanical and electrical properties. 3. Disadvantages of foaming. Small mechanical strength, low wear resistance and heat resistance. 4. Principle of foaming 1. Physical foaming is In the process of plastic extrusion, gas or liquid is injected directly (the manufacturing method of physical foaming of foaming insulation is to use gas without loss to use foaming Qi), so the disadvantage of chemical foaming agent is eliminated, that is, there is no residue or water produced by chemical foaming method in the insulation, which greatly reduces the dielectric loss of the insulation. Physical foaming can eliminate many processes of chemical foaming The foaming degree of chemical foaming insulation is only about 40.2. The physical foaming insulation material is due to the composition of basic resin insulating plastic, foaming agent and nucleating agent. The physical foaming insulation material is mainly used in polyethylene and also in the physical foaming of fluoroplastics. When the polymer is used in the physical foaming, the PE insulation material should be When the foaming agent is mixed with nucleating agent, it is injected into the molten polymer at the same time and precipitated from the melting state so that the condensation center and bubble nucleating agent can be produced continuously during the extrusion process, which can make the size and distribution of bubbles uniform. 3. Nitrogen foaming is to start the injection pump by compressed air, boost the pressure of nitrogen high-pressure pump under a certain pressure, control it through the constant flow valve, and then start the injection pump from the steady flow valve The nozzle injects nitrogen into the extruder when nitrogen ‘(under high pressure, it sprays into the molten polyethylene in the extruder like a mist) and nucleates with the nucleating agent in the polyethylene. After extrusion, the main process of forming foam insulation nitrogen foam in the air is dissolving nitrogen into the molten polyethylene PE to form a micro bubble structure. In the screw cylinder of the extruder, a small amount of nitrogen is formed After the PE material of the nucleating agent is fully plasticized by heating and stirring, nitrogen is injected. 4. In order to facilitate the formation of foam pores, a certain amount of nucleating agent is added to the PE material in the physical foaming process. The main components commonly used are azo-2-wash-amine. 5. Process equipment and process Design 1. The stability and sealing of the high-pressure nitrogen injection system range of 50700bar are good. 2. The preheating equipment of inner conductor should have enough power to realize The regulating range of conductor temperature is 50 ° C at normal temperature. 3. The traction of core wire should be stable and the cooling water tank should have enough length. 4. Because the nucleating agent decomposition induction period is long and there is still residual after sudden extrusion, the die temperature should be low, otherwise, the inner part of insulating layer in high temperature environment will show excessive growth of blisters, which will lead to blister rupture and large blister
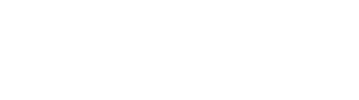
Your search is over as Graphene New Material(GNM) not only provide you with the latest graphene soccer shin guards, 3mm thin two-sided magnetic white board, various polymer-modified materials related to foaming, various compatibilizers related to compounding, various equipment and production lines related to it