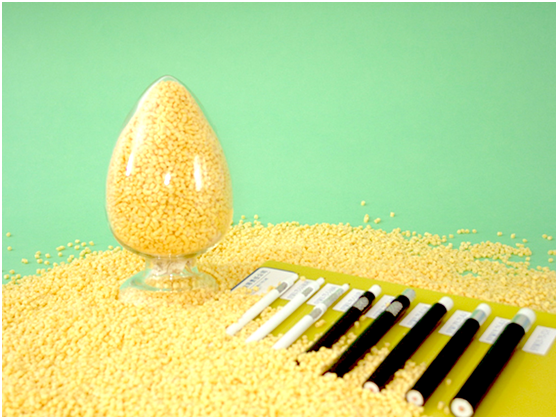
In the foaming process or polymer materials, the honeycomb or porous structure is formed by the addition and reaction of physical foaming agent or chemical foaming agent. The basic steps of foam forming are to form a bubble core, to grow or expand the bubble core and to stabilize the bubble core. Under the given temperature and pressure conditions, the solubility of the gas decreases, so as to reach the saturation state, so that the excess gas is eliminated and bubbles are formed, so as to realize the nucleation.
Making a general term for molding methods of foamed plastics. According to the classification of foam plastic manufacturing methods, they can be classified into two categories: the method of making foam plastics by one process after matching the raw materials of foaming plastics, is called one-step foaming method, also known as direct method, polyurethane foam plastic is its typical representative; the method of making foam plastics from two processes is called two step foaming method, also known as intermittent method. In the two step foaming process, the former process is called pre foaming or pre foaming, when the foam or beads are not fully expanded and the density is higher, so the beads are granular. The latter process is called post foaming or two times foaming, making the final foam product with full expansion and low density. Polystyrene and polyethylene foam are manufactured in this way. In industry, the foam forming methods are classified as follows: (1) continuous foam forming by calendering, extrusion or conveyor belt, etc.; and (2) intermittent foam forming by injection molding to produce the final shape of foam body one by one. (3) According to the use requirements, the liquid or particulate raw material complex is injected into the mold to make it foaming, which is called field foaming molding.