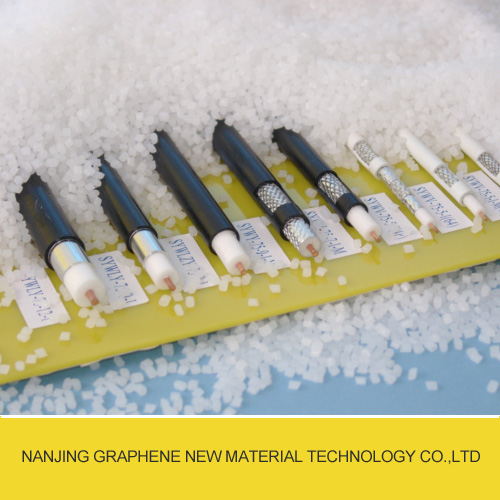
Compared with chemical foaming, the foaming degree of physicalfoaming can be improved obviously. Taking PE as an example, thehighest foaming degree reached by chemical foaming is 50%, andthe maximum foaming degree reached by physical foaming is 80%.
In the production of cable products different, generallyreached the foaming degree is different, for example: the .chemical foaming, the highest foaming degree of 40% telephonecable; the physical foaming, the highest foaming degree of 60%telephone cable, the hi ghest foaming degree is 65% in the data .cable, the hi ghest foaming degree is 72% 75% with mini the shaft of the cable, the highest foaming degree of 78% coaxialcable, the hi ghest foaming degree is 80% RF cables.
At the same time, foaming degree to improve the physical foaming process has many advantages, including: improving the speed of the production l ine, reduce the use amount of the copper material and an outer shield insulating material from the weight, and further reduce production costs.
Assuming that solid, chemical foaming and physical foaming are used to produce a commonly used coaxial cable (according to the French standard type A2) to compare the main advantages of physical foaming see table 1. Three common coaxial cables(shown in Figure 1) have the following properties: the, innerconductor uses copper wire phi 3. 3mm; the impedance is 750hms;the insulating material is PE; it is suitable for the 80mm extruder , (for comparison of producti on speed).
As can be seen from the above comparison, when using the Physical Foaming Insulation Materials Mixed With Nucleating Agent, a large amount of insulating materials and shielding materials can be saved, and the transmission performance and the production efficiency of thecable can be improved.